Canada’s mining, energy, industrial machinery, and pharmaceutical sectors are major contributors to the national economy, employing hundreds of thousands of workers. Increasingly, these sectors are turning to contractors to meet their business needs.
Contractors Integral to Operations
Cognibox’s new whitepaper, Zero Harm: 7 Key Insights for a Safer Workplace for Contractors, consolidates thought leadership from senior health and safety experts overseeing complex and dangerous operations in mining, mineral extraction, and pharmaceuticals for some of the largest corporations in the world. It suggests that this reliance on contractors is only increasing. At the companies we engaged for the whitepaper, often there are more local contractors working on a jobsite than employees.
“The mine is an active project, with 80% of the workforce made up of contractors," said a safety director at an iron mine who participated in Zero Harm. Another participant, an occupational health and safety manager at a major gold mining firm, punctuated exactly how integral outside workers are in mining, saying “Without contractors, we would cease to exist.”
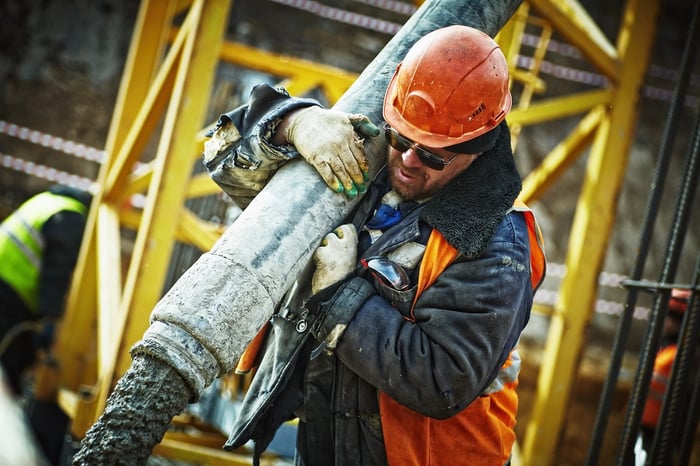
Contractors Face Difficulty Assimilating
This high dependency on outside workers complicates operations considerably and requires systematic contractor management to ensure everyone’s safety. Due to limitations in reporting, detailed statistics around increased risk for contract labour are limited, but their vulnerability is clearly elevated.
Contractors are often not fully immersed in the safety culture and may not be familiar with work sites, practices, and procedures. Unlike employees, they may also change jobs frequently, never fully becoming assimilated to one company’s culture of safety. In addition, the safety standards and protocols of the contractor may not be aligned with that of the hiring organization.
Even organizations that are committed to contractor safety face obstacles. A rigorous approach to safety can impose significant costs on hiring companies, often requiring substantial paperwork and bureaucratic procedures to ensure contractor qualifications and credentials are up to date.
This combination of factors creates dangerous gaps in behaviours, knowledge and skills that make project sites even more dangerous, especially for the contractors themselves.
Take Canada’s oil sands, for example. As with most other industrial sectors, production in the oil sands relies heavily on contractors. “While safety events for core staff have improved, changes are slower for contractors who can make up as much as 40% of the workforce at oil sands companies,” said a health and safety manager from a major synthetic crude oil producer who participated in Zero Harm. Contractors are also involved in incidents 2-3 times more often than full-time employees.
Clients Corporations Must Take Responsibility into Contractors Safety
Virtually all safety leaders we engaged for Zero Harm agreed that as part of a contractor management program, it is ultimately the responsibility of the hiring company to ensure the safety of everyone on a job site.
Although contractor safety remains a philosophical obstacle for many organizations, advancements in technology can dramatically ease administrative challenges and reduce costs, giving the senior management team a clear and compelling incentive to invest in a robust safety systems. Over time, these investments in technology can encourage positive behaviour and sustain a strong culture of safety.
Contractor management and safety is an important subject in many industries. From mining to energy to pharmaceuticals, creating a safe workplace for contractors is paramount, not just for worker health, but for business success as well.
Our new whitepaper, Zero Harm: 7 Key insights to consider in creating a safer workplace for contractors, is built on the perspective and experience of health and safety leaders. It discusses challenges and reflections and offers solutions and best practices on how to improve worker health and safety.