Technology is completely transforming sectors, and disrupting entire business models. The impact of these technological and process changes are headline news in some sectors, and although the change in mining might be less headline grabbing, the impact is no less profound. The leading innovations in mining will not only make exploration and excavation of materials faster and cheaper, but also increase safety and reduce environmental impacts.
The mining industry faces a number of challenges as worldwide prices fluctuate, firms are held more accountable for the safety of their workers and contractors, and the performance of every single mine in effectively engaging local communities and protecting the environment is more heavily scrutinized than ever before.
We break down some of most significant innovations in mining that are transforming the industry and keeping workers safe:
Mining Simulators
Similar to training airline pilots, mining simulators are becoming more common and put workers in a controlled and immersive virtual environment. This allows them to test their skills and make mistakes where it doesn’t matter before going into an actual mine where they will be exposed to the risks of operating equipment in tight and challenging locations underground. 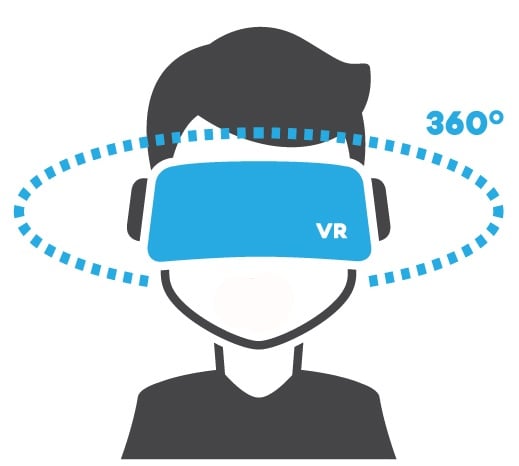
Simulators place workers in practical situations they are most likely to encounter during a typical shift, including emergencies that help them to make sure they have their reactions and responses finely tuned. Simulators are excellent teaching tools that can identify gaps in knowledge and skill, especially when bringing in outside contractors, without exposing miners to hazardous environments they have yet to experience.
Contractor Management
There was a time when mining firms directly employed hundreds of workers on a mine. Technology and the evolution of the industry have changed that, as mining companies rely more heavily on contractors to undertake work within the mine site. With different people coming and going this can be at best an administrative headache, and at worst a significant safety risk. Making sure that contractors have all their training and credentials up to date used to be an exercise in back and forth emails and searching files for documents.
Now platforms like Cognibox set out expectations around each site, enable individual contractors to have all their documents in one digital location, and if a contractor does not have what is required they will be automatically locked out of the site until they do. Discover how Cognibox helped a Canadian mining industry leader reach a goal of 0 workplace accident while managing many contractors.
Underground Telecommunications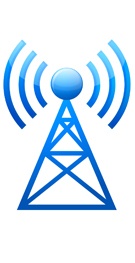
Until wireless technology arrived, communications between miners was primarily through whistles. Today, miners can set up a wireless network thousands of feet underground and use Skype-type telephones to communicate not only with each other, but also to a control site above ground.(1) Coordinating emergency responses has also become safer and more effective. Barrick Gold’s operations in the Cortez mine in Nevada, rely on an underground wireless network, not only for communications, but to collect key data on equipment usage and personnel, and respond in real-time for maintenance, repair and emergency communications with surface and the mine rescue team.
Personnel Tracking
There was a time not long ago when miners heading underground would place a token on a board before entering the mine known as “brass in and brass out”, and remove it once they came back to the surface. That helped to get a sense of who was in the mine, but had little benefit beyond that.
Today, Radio Frequency Identification (RFID) tags, which emit radio frequencies, are secured to workers’ uniform, and can easily track their whereabouts in real time. This eliminates site downtime, human error, and the need for unnecessary search-and-rescue operations. And because a miner’s location is always known, emergency responses are faster, saving valuable time in case of an incident.
Microseismic Monitoring
Vibrations resulting from mining operations, especially blasting and excavation, put significant stress on the ground, leading to microquakes that can put operations and people at risk. Effective and reliable monitoring of changes to the site’s structural integrity is critical to determining if the risk level at a mine has been elevated due to ongoing mining activities. Today, site operators can use microseismic monitoring to locate these microquakes in 3D, gauge their severity, determine if site safety is at risk, and can take proactive measures before a catastrophic event.
Drones
Mapping poses unique challenges underground, where areas can be inaccessible, and pitch black. Drones controlled remotely can map tunnels in great detail, including capturing the texture of the walls, offering planners much higher clarity and reliability. Data captured by robots can also be used to create rich visualizations, minimizing the need for potentially risky trips underground, and creating opportunities to share data on the mine with off-site personnel.
Protective Equipment
Wearable technology, from gas detection devices, to garments that cool, personal protective equipment (PPE) has seen major advances in recent years.
- Noxious gases produced by internal combustible engines and blasting, pose lethal hazard to miners underground. Gas detection sensors can indicate in real time when the concentration of poisonous gases exceeds safety guidelines and notifies them to leave the site immediately.
- Workers must also contend with heat; temperatures in underground mines can often reach 60°C, (140°F). Miners can now wear cooling vests and other garments that regulate temperature, and provide warnings if their body heat reaches unsafe levels.
Mining Data
In conjunction with innovative equipment and technology, data can be used at all stages of mining, from recruitment of qualified workers, to predicting when a machine is likely to fail. Both factors can be pivotal in ensuring safe and efficient operations.
Mines have become data rich operations and all that information can help to bring benefits across many areas, including improving logistics, which remains the most inefficient part of the entire mining process, and identifying risk factors to keep people safe.
Where to start?
Did you notice these innovations have one thing in common?
All of them are health & safety related. Health and safety is a big concern in the mining industry. The right technology, the right equipment and a appropriate training can ensure good practices and reduce risks. Is your company in good shape? Cognibox's team can help you to know where to start.
- http://www.mining.com/carlson-wireless-develops-cost-saving-wireless-link-for-femco-emergency-phones-used-extensively-in-the-mining-industry/