Almost a quarter of a million people miss work due to workplace injuries each year in Canada
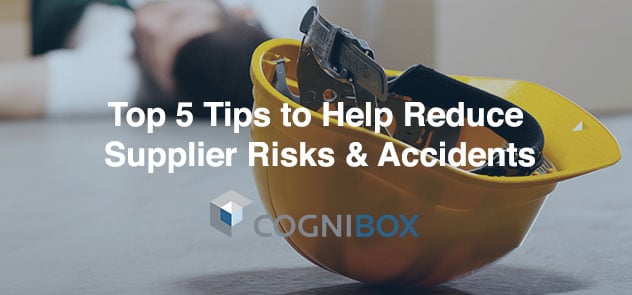
More and more companies rely on suppliers to deliver critical components or services that they once used to deliver themselves. There are many advantages to getting that outside expertise, but there is increased complexity and additional risk. Responsibility for the well-being of employees now extends to the employees of your suppliers.
That responsibility cannot be outsourced and the biggest companies are increasingly being held accountable for any incidents or accidents in their supply chain. The economic impacts can be big as well with the International Labour Organization estimating that workplace injuries and work-related illnesses costs add up to four percent of gross domestic product a year.
We are seeing improvements. Year-on-year the number of workplace injuries leading to missed days at work keeps dropping. In 2014 we saw the lowest total ever in Canada, at less than 240,000; a fall of 100,000 over the last ten years. It is still over 650 injuries or illnesses per day and any such event can severely impact the life of the person hurt, and companies are rightly working hard to make sure suppliers are doing all they can to reduce the number of incidents.
Cognibox has been working closely with companies to help reduce incidents in supply chains and was recently recognized as the best contractor management solution in the country by the readers of Canadian Occupational Safety magazine Canadian Occupational Safety magazine. To mark that honour, we have compiled our top five tips to help organizations lower the number of incidents and accidents amongst suppliers.
1. Hire the Right Contractor
While this may sound simplistic, there are a lot of factors to take into account when choosing the right contractor. The right contractor is not always the one with the best price. Knowing their history, qualifications and even the type of equipment they use, will help you make a more informed decision and give you confidence. Establishing standards can help provide clarity around the expected safety requirements.
2. Visit Your Supplier Sites to Assess Safety
Your company is only as safe as its weakest link. That means if one of your suppliers is lagging in health and safety, it can impact you. Unfortunately, you can’t always assess your suppliers’ safety compliance over the phone or email. Whenever possible, visit your supply sites. Take tours, speak to the workers and get a first-hand view of any issues that can hamper safety, Remember, if one of your suppliers has an onsite accident that forces shutdown or slows production, this disruption has a domino effect on your deliverables.
3. Train all Contractors in Emergency and Hazards Procedures on your Sites
Some contractors will never work on your site but those that do should be treated as new employee hires when it comes to health and safety precautions. This should be done in all cases, whether a contractor is on your site for a day or a year. Workers who are not trained in a site’s safety procedures can be left more open to accidents and, if an incident occurs, their ability to get correct or speedy care can be compromised. Because you will not be able to prove due-diligence, this will put your company at risk of lawsuits, criminal charges or both.
4. Track Contractors’ Whereabouts
Asking contractors to check in and out of your site can be cumbersome but knowing where everyone is in the event of an accident is crucial. It’s also important for your workers to know who else is on their site or in an area where they are working so they can take that into consideration when operating equipment or performing a task that might leave others nearby in some kind of danger.
5. Use the Right Contractor Management Solution
Firms that hire contractors can specialize in a variety of sectors from agriculture to zinc mining. They don’t always specialize in managing contractor compliance. With so many aspects to consider, including correct qualifications and certifications, individual insurance policy expirations and safety training requirements, it can take your team a great deal of time to ensure you have fulfilled your due-diligence obligations. The explosion in the amount of data available, and what is required to ensure suppliers’ employees are well protected, can no longer be done without the right tools.
We hope these 5 tips will be helpful to reduce the number of work accidents caused by suppliers and contractors on your operation sites. If you wish to learn more about the best practices in contractor management, download our complete guide on the subject.